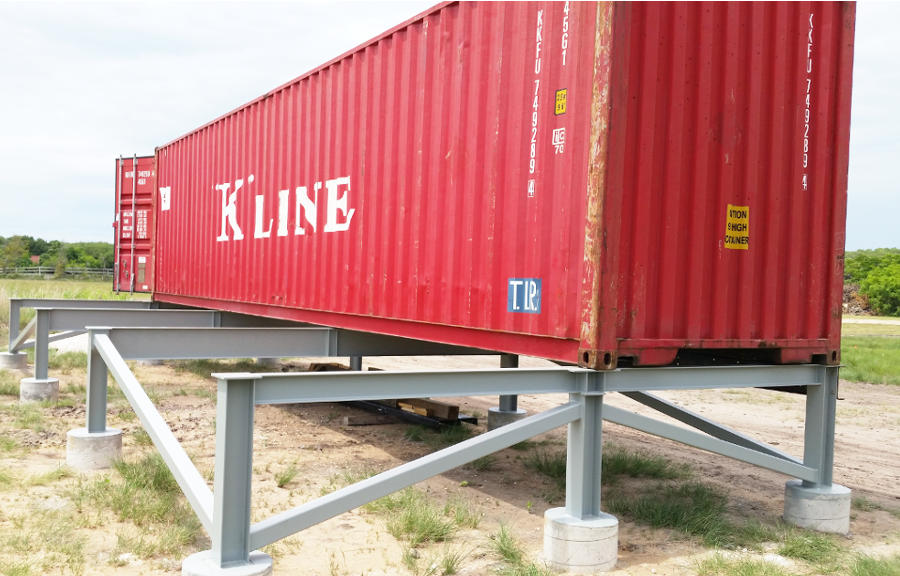
The Conex Slide
Ah, chickens. After being released into their new chicken run on Friday, a lot of time was spent over the weekend just watching the little peepers do their thing. There is something very relaxing about chickens maintaining proper hygiene. Have you ever watched a chicken scratch? I am not talking about seeing a chicken scratch, I am talking about intently watching how they scratch.
Satisfying was it not? How does a chicken even know where it scratched? To the untrained eye, it looks as though they randomly scratch and peck. If they find a bug, yeah. If they don’t find a bug, yeah. Chickens are simple.
Chickens scratch to find dirt to dust their feathers. Dusting aids in the removal unwanted bugs. Chickens scratch in the same dirt to aid in their food consumption. So tell me how they can remove unwanted bugs but then eat the bugs they want from the same patch of just scratched dirt. It is a fine line they walk. I know, I know. Don’t over analyze it, they are just chickens. They seem to enjoy the scratching either way. If the chickens are happy, then all is good.
Wednesday morning the boys left bright and early yet again for big city #2 for the third conex box. This was a very exciting moment. Yes, the boys have already gone to big city #2 for the two other conex boxes. So what could be so exciting about this trip and third conex box? Easy. It is the first conex box for creating the 16’x40′ shop.
Unlike the others, this conex box was picked up at a different location just outside big city #2 down this long beautiful country road. Along the side of the road where the grass met the road bed was all these funny little dirt mounds. Whatever creature builds these has some fantastic artistic ability. They remind me of Easter Island statues.
The drive in went wonderfully. The drive out, not so much. There had been some major rains over the weekend and the roads had not dried out. Conex boxes are not really heavy in the large scale of things but it was too heavy for the road bed. Sorry, the road beds were torn up trying to get out.
Driving down this long drive seemed surreal. To look around all one saw was grass fields lined with thick trees, the driveway, the crafted fence, and the metal shop in the far distance. If you didn’t know a bustling city lied beyond the trees you could get lost here. However, leave the safety of the cab of the truck and one could hear the roar of the highway. Bummer. Oh well, at least it was pretty on the eyes. Or so I have been told. The boys were picking up a box, I was at work.
Friday the Doubter came down to help unload the third conex box. Having been the third, it would seem like Boxes in Fields should have the system down already, right? How wrong you would be. This third box is being slide over onto the subframes. Since there were doubts as to how well the Planner’s “simple slide over and off” procedure would work, Friday afternoon was spent getting as much prep work done as possible. Nothing wrong with being ahead of the game.
Before this post goes too much further let me give a breakdown of how this conex box will be moved. It won’t take long. It is as easy as one-two-three. At least that is what the Planner keeps telling me. Step 1) Raise conex box on the trailer to match the height of the subframes. Step 2) Attach a ramp to the subframe. Step 3) Slide conex box onto the subframe. That’s it. Easy peasy he keeps telling me.
Saturday morning came unexpectedly quick. Somewhere between 930pm Friday and 630am Saturday, time sped up double fast. I swear. In retrospect, the time warp worked out just fine as I was more than ready to start the day and get this craziness over with and done.
Right off the bat the brackets that were built, as designed to support the ramps, didn’t fit. This is not a good sign. Bad omens should never start a project. They can occur during a process but should never lead a project. Stomach cramp #1, ugh.
After a quick modification, the brackets were easily attached. If it weren’t for the torch marks and slag build up, the final product looked like it was created to fit. Of course, neither the Planner nor the Doubter was happy with the final results because time was not spent to make them look professional. There is no time for grinders and whatnot for cosmetic appeal. These are not even staying. They are simply a means to an end.
The brackets are bolted to the channel and the channel is bolted to the subframes. In case you are wondering, these are not your standard run go the mill, household bolts. Come to think of it, I don’t even know if the local home improvement store sells bolts of this industrial grade. Bolts used were 5/8″ grade A. Was it an overkill? Maybe. With projects of this nature, it is better to err on the side of safe. Didn’t want a bolt shearing during the push over and off process. Sheared bolts are a scary thing.
Bolts bolted? Check. Doubled impacted for extra safety? Check check. Slide the pin in place and let’s move on to the next of many, many steps. Time’s a ticking, it is 9am already. Good grief. Where did the last two hours go?
The last easy step was the alignment and placement of the box next to the subframes. The pad in which the four corners of the box are placed on is 6×6 in width. The width of the I-beam running between the two pads is only 3″ in width. Aligning the box before sliding over is important as there is not a lot of fudge room to move back and forth to straighten out once the shipping container in on the substructure.
The box must be slid across evenly. Rusted metal corners on boxes and freshly painted subframes. Nothing about that combination says slide easily to me.
Raising the box to the desired height was thought over and mulled over and debated over for what has felt like weeks. WEEKS! Neither the Planner nor the Doubter were sure as to how much the conex would need to be raised off the gooseneck to slide over onto the substructure as there were too many factors to consider. How soft is the ground since all the rain and dirt work? How much will the channel flex? How this and how that? What about this and what about that?
In fact, this debate was still under consideration while straps were being removed. How can the Planner have failed me? He is SUPPOSED to have EVERYTHING planned down to crossing the T’s and dotting the I’s. The straps were removed and stored and it was still being discussed! There was nothing left to do except to do it.
And do know what the final decision was? To play it by ear! Are you kidding me? The Planner’s final answer Alex is “to play it by ear”. Ugh. This is not what I wanted to hear. Stomach cramp #2.
What was used in the end was a hodge-podge of tools. There were two notoriously dangerous high lift jacks, two 20 ton bottle jacks, stub pieces of leftover 12×12 piers, 2×4 pieces, 1×2 pieces, and lots of trial by error. Yes Planner, your lack of planning worked fine. There I said it.
And if I am honest, I was only worried once during the lifting stage. Just once. And what caused this moment of worry? I swear the box shifted/waivered/veered to the driver’s side when lifting with the high lift jack. Nobody else saw it but I did. It did and that is my final answer, Alex. Stomach cramp #3.
Next step, please! Let’s get this show on the road. The sooner it is done, the sooner it will be over. The frame channel ramp was attached to the modified brackets and the conex box was lowered onto the ramps. Going down was so much easier than going up. Nice and smooth. No wavering. No scary, temperamental high lifts. Just a slow, gentle descent. Why is always like that?
Oh, wait. It’s not. With the full weight of the conex, the ramps bent like a stiff fettuccine noodle. A dry noodle has some bend before it breaks completely and that is what happened with the channel too. But it didn’t break, so as with all things at Boxes in Fields, it was modified on the fly. Aha! Another rummage through the One Man’s Trash pile resulted in two junk 12×12 piers. These were cut to fit under the ramp to help support the weight. One never knows when a piece of junk pier will be needed.
Up and down went the conex again. Damm, it was still bending. Add some 2×4 pieces and it was set. Alright let’s slide.
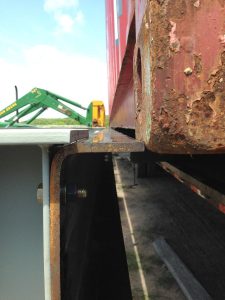
Frame channels were painted with some very slick paint to assist with the slide. This was both good and bad. It required just the slightest nudge from the tractor to move. It also has nothing to stop it if pushed too hard. Zing! Stop! Holy Crap! Stomach cramp #4.
It is a good thing none of us can measure and the ramp and trailer were still too low. Once nudged, the box slide until it came in contact with the first channel. Less than 1/8″ was the stopping point as it turns out. And it stopped with a deep resounding thud.
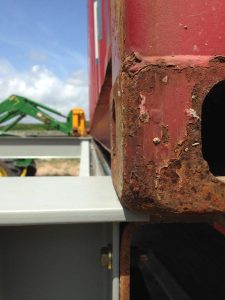
To step over the channel high lift jacks were used to raise the conex while pulling with the tractor. Pulling is not as smooth but it has a major advantage. Pulling allows the tractor forks to stop the conex from sliding too far again. Stopping is GREAT! Stopping is not overrated. Not overrated at all. After being lifted onto the channel, the same process was used to step onto the subframe itself. Straight from the start the box was already off centered. Oh well, nothing goes as planned completely. It just goes.
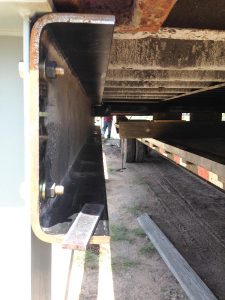
From underneath, everything looks great. The channel attached to the subframes is not bent, the ramps are working very smoothly, and all that is left is to move the conex onto the frame itself.
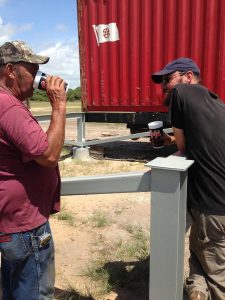
After a break of course. Wouldn’t want to get done too quickly. It is only noon. Noon-twenty. Yes, I have been told I can be a slave driver. Fine, fine, a quick break for the worker bees. Oh wait, that’s me!
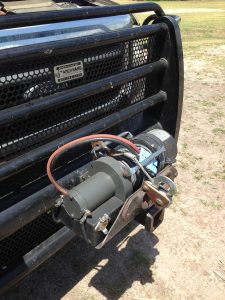
Over tasty beverages of choice, it was discussed as to how to keep the conex from sliding off to one side or another. What better way, without having to really do anything, is with the use of a winch. The box would move and the winch would lose tension. The winch was reattached, the box moved, and the winch would lose tension. Repeat, repeat, repeat moving just inches at a time.
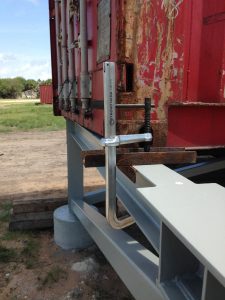
But you know what? Inches at a time worked just fine and the box moved right over. Yes, moved. Not slide. Slide implies smooth movements. As previously stated, the corner of the boxes are rusted and the frame is rough paint. The results of the combined two are friction. Friction resulted in the Doubter pushing instead of pulling. To help in the stopping process and to relieve some of my stomach issues (#5, by the way) brackets were attached to the frame. Now the box could only move so far.
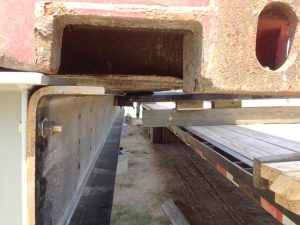
Movement across the subframes was erratic as best. Some were smooth, some were rough. Some went as directed, some just went. All was going as smoothly as it could go, really. Little by little, inch by inch it went. Right up until the Doubter ran out of push with the tractor. The forks on the tractor were too short and he couldn’t reach across the width of the trailer to conex box to continue pushing. There was some serious head-scratching. How to move the box? Can’t be pulled. Can’t be pushed. Think, think, think.
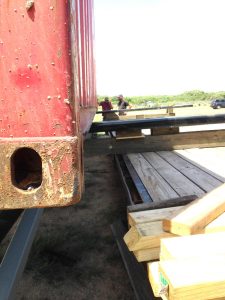
Think, think, think….. “Hey, why don’t you use the channel ramps from the storage box?” These were just like the channel the box was sliding across and twice as long as the forks on the tractor. They could easily be attached and secured to the forks and then the tractor could continue its pushing technique. If it ain’t broke don’t fix it. Sometimes I even impress myself with my ideas of simplicity.
A couple more bumps and the conex was done. Well, not done, but in place. And guess what? It was only noon-fifty eight. 12:58pm! Not bad for a half day worth of work.
Walking around talking in the sheer wonderfulness of the first conex box on the subframe it was noticed the box did not touch the middle frame supports. Was this bad planning? Were the footing not poured correctly? Were the frames not level? How bad will this affect the overall result? Chill, woman! “The conex box will flex when the heavy tools and machinery are added. It was planned this way. ” or so I was told. Apparently, conex boxes are designed to carry their entire weight on the four corners. Huh. Who knew? Not me. 60,000 lbs on four corners. That’s some crazy planning.
The last step for the day, to center the boxes on the subframes. This was by far the most nerve-wracking moment. There was nothing to stop the box from moving too far. It would stop when it stops. Stomach cramp #6.
A few very, very GENTLE nudges with the tractor and some weld tacks to the corners and it was done. Can you believe it? It was a mere 1:30pm. DONE! There was a whole afternoon left to do whatever. There was time to simply observe the beauty that surrounds.
Flowers to marvel at…..
Itty bitty, teeny tiny praying mantis to coo over….
Completed, raised conex box to admire….
And lots and lots of diet drink to enjoy from the top of the conex. What a view it is too! (Panoramic views are often turn out wired not the video was much better). Can’t believe me and my stomach made it through. But done is done, right? Now, the fourth box. Or second box, depending on how you look at it.